Nuovo Impianti di Estrusione della Plastica
L’impianto è costituito da una serie di elementi, connessi tra loro, in modo da garantire un perfetto funzionamento nel pieno rispetto delle normative vigenti in materia di sicurezza per l’operatore e l’ambiente circostante (Direttiva Macchine 89/392 CEE, 91/368 CEE, 93/44, 93/68 CEE).
L’estrusore è costituito essenzialmente da un cilindro ed una vite che ruota al suo interno. Durante il funzionamento, il materiale introdotto è plastificato grazie al calore fornito dalle resistenze elettriche (poste intorno al cilindro). La regolazione a regime della temperatura è affidata alle resistenze e ventilatori che, intervenendo periodicamente, mantengono costante la temperatura in ogni zona in cui è diviso il cilindro di estrusione.
Durante la lavorazione avviene l’eliminazione delle sostanze volatili (prodotte durante la trasformazione) per mezzo di un doppio degasatore.
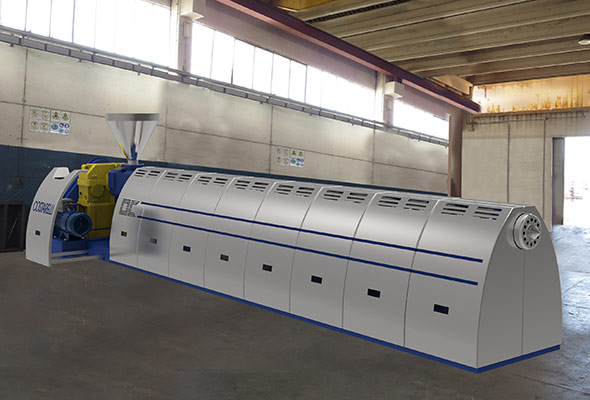
Descrizione dei componenti principali della macchina
- Il basamento è costituito da lamiere elettrosaldate; su di esso sono montati il motore, il riduttore e il cilindro di estrusione.
- La trasmissione del moto, dal motore al riduttore, avviene per mezzo di cinghie trapezoidali protette da appositi carter imbullonati alla struttura.
- Il motore elettrico è di tipo a corrente continua consente, al variare del carico applicato all’asse della macchina, un proporzionale aumento di corrente e quindi un’adeguata variazione del numero di giri della vite di estrusione nelle diverse condizioni operative.
- Il riduttore è del tipo ad assi paralleli realizzato con ingranaggi di acciaio cementati, temprati e rettificati protetti da una carcassa in ghisa. Il riduttore è dotato di una campana di raccordo, mediante la quale si caletta al cilindro di estrusione; all’interno della campana è montato un cuscinetto assiale a rulli, orientabile, in grado di neutralizzare il carico assiale della vite di estrusione.
- Al riduttore è applicato un impianto di lubrificazione forzata con scambiatore di calore. Ciò garantisce la lubrificazione continua dei cuscinetti e il mantenimento della temperatura entro i valori prestabiliti dai produttori dei lubrificanti.
- La vite di estrusione è costruita in acciaio speciale trattato termicamente, nitrurato e rettificato, essa è responsabile del trasporto del materiale da estrudere.
- Il cilindro di estrusione è ricavato da un tubo di acciaio speciale nitrurato con superficie interna rettificata.
- Le camere di degasaggio hanno il compito di eliminare l’aria e/o gas che si sviluppa, durante la lavorazione nell’impasto, prima di essere tagliato.
- Il riscaldamento del cilindro è avviene in zone ed è realizzato mediante resistenze elettriche (a fascia) montate attorno al cilindro, le quali sono isolate con materiale ceramico e ricoperte da un involucro per la protezione del personale addetto e per il recupero del calore. Ogni involucro è costituito da una lamiera in acciaio inox riflettente.
- Il raffreddamento è richiesto in diversi punti della macchina:
- nelle zone lungo il cilindro, tramite ventilatori, comandati dal quadro di controllo, ciò permette una corretta regolazione della quantità di calore necessaria alla lavorazione del materiale;
- nella zona di alimentazione del cilindro tramite un sistema di raffreddamento ad acqua;
- nello scambiatore di calore dell’olio del riduttore;
- L’acqua usata per il raffreddamento non è contaminata, così può essere scaricata o riciclata senza subire trattamenti di depurazione.
- Il quadro di comando (IP 54) è costituito da un armadio metallico in cui sono posti tutti i componenti elettronici della macchina esso è dotato di chiavi (per la sicurezza) che dovranno essere in possesso di personale altamente specializzato. Sul quadro sono presenti oltre agli usuali dispositivi di comando (pulsanti di Start e Stop dell’estrusore, un selettore ON/OFF per le zone di riscaldamento ed uno per il sistema di degasaggio) anche quelli di controllo del sistema (dispositivi digitali ed analogici collegati coi rispettivi strumenti di misura: trasduttore della pressione in testa, un contatore dei giri della vite dell’estrusore e, per ogni zona di riscaldamento, una sonda amperometrica ed un sensore di temperatura) e di sicurezza (pulsante di emergenza, una sirena di allarme per la massima pressione in testa). Un PLC gestisce automaticamente in modo sequenziale l’avviamento e lo spengimento estrusore.
- La tramoggia di carico è realizzata con una lamiera sagomata ancorata al collettore tramite una serie di viti.